
A2L: New Refrigerants, New Tools, New Techniques
April 29, 2025 | By Ian McTeer
The introduction of A2L refrigerants into the market will require some modifications to how HVAC techs get the job done.
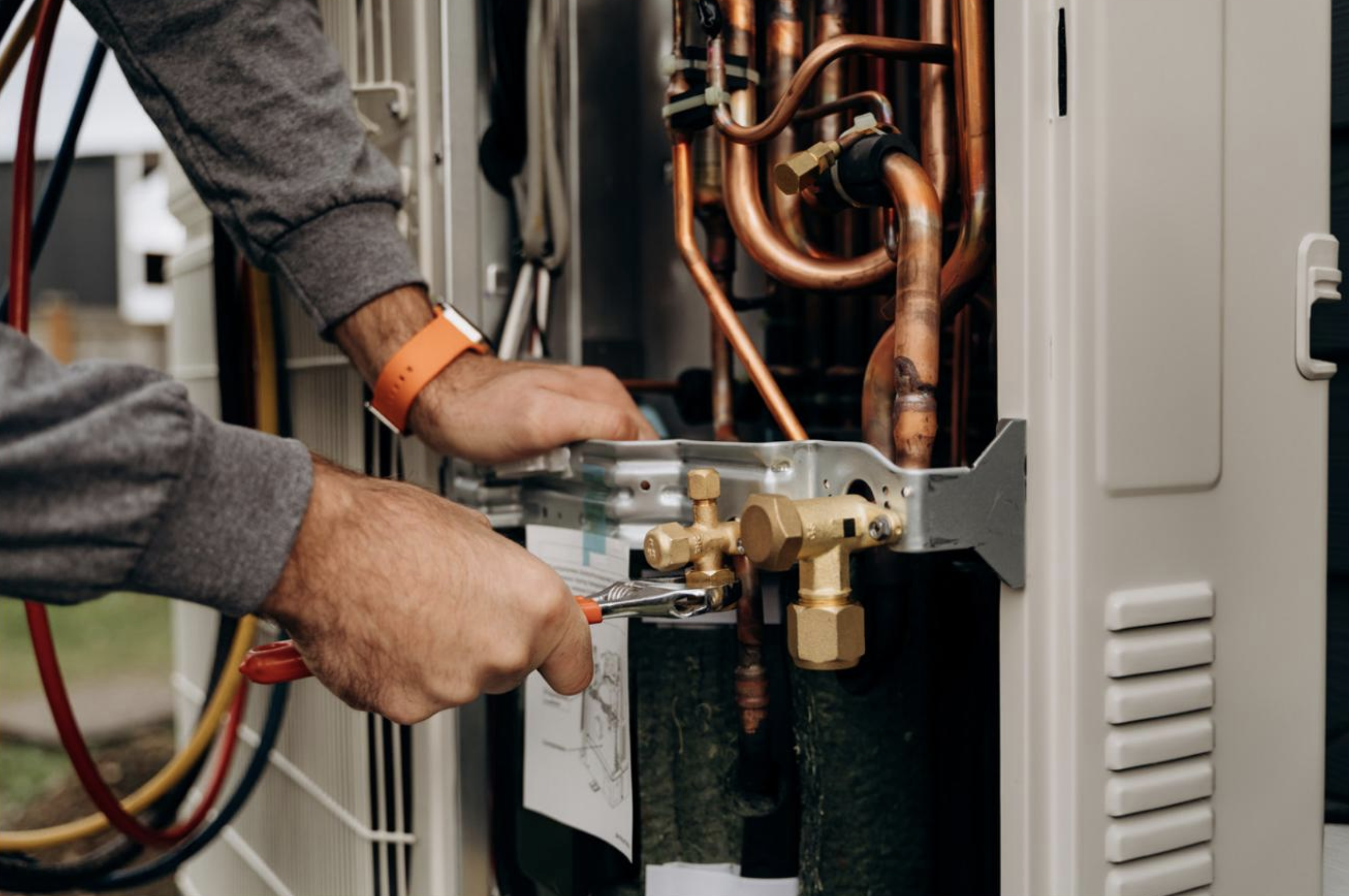
(Photo: Vadym/Adobe Stock)
As the clock struck midnight on January 1, 2025, a significant transformation took place in the residential air conditioning and heat pump industry in the U.S. Manufacturers must now adopt lower global warming potential (GWP) A2L refrigerants to align with stringent environmental regulations and sustainability goals.
To date, large volume residential manufacturers such as Lennox, Trane and Carrier have opted to use R-454B, while Daiken/Amana/Goodman will utilize R-32. These new refrigerants, characterized by their reduced impact on global warming, will undoubtedly reshape the universe of HVAC systems.
However, this transition is not merely about substituting old refrigerants with new ones. It necessitates an evolution in tools, techniques and safety protocols, prompting technicians and industry professionals to adapt to the changing dynamics.
This article delves into the implications of this shift, exploring the benefits and challenges posed by the introduction of A2L refrigerants and what it means for the future of residential cooling and heating solutions.
The Refrigerants
Yes, it is true, the latest lower GWP refrigerants are mildly flammable. At the same time, it is important to consider the lower flammability limit (LFL) of these A2L refrigerants. LFL is the minimum concentration of any refrigerant that is capable of propagating a flame under specific test criteria. Since every flammable gas requires oxygen to burn, too little gas or too much gas (upper flammability limit), although mixed with oxygen, will not burn.
For example, R-32 has an LFL of at least 14% in air, any less gas and the lean mixture will not ignite. The upper limit is 31% in air, any additional gas (rich mixture) will not ignite. Only mixtures between 14% and 31% can ignite. The LFL of R-454B is 11.3% by volume in air, its UFL is 23.6%. By contrast, natural gas (a hydrocarbon) burns between 5% LFL and 15% UFL.
Thus, a higher LFL means a higher concentration is necessary to create a flammable situation. Another important related flammability metric is the Minimum Ignition Energy (MIE). These values indicate the minimum energy required to ignite a flammable mixture of refrigerant with air under specific conditions.
For example, R-32 has an MIE of approximately 8.0 millijoules (mJ) whereas R-454B is approximately 10 mJ. By comparison, natural gas MIE is about 0.25 mJ, even gasoline is about 0.24 mJ.
Both R-32 and R-454B have higher MIE values compared to A2 and A3 refrigerants. Remember, A2Ls do not contain hydrocarbons. R-32 is a pure HFC while R-454B is a zeotropic blend of two refrigerants: 68.9% R-32 and 31.1% of R-1234yf.
The lower flammability limits of A2Ls are roughly 10 times higher than that of an A2 such as R-152a or any A3 such as R-290 or R-600a. Thus, something like 10 times the amount of liquefied gas would have to leak from a cylinder in order to create a flammable mixture in air.
Minimum Ignition Energy values are in the order of 100 to 1,000 times higher than A2 and A3 gases. Isobutane and other A3s can be ignited by a static discharge, whereas A2Ls typically will ignite only in the presence of an open flame or active fire. And a lower burning velocity (BV less than 10 cm/sec) means the potential for an explosion or flash fire is much less likely.
The Tools
Installation processes related to equipment containing A2Ls are nearly identical to industry standards in use today. However, A2L refrigerants and their unique, but not necessarily burdensome, characteristics will require contractors and individual technicians to invest in several new tools and to implement some upgraded techniques into daily routines.
Figure 1 is a chart comparing tools, equipment and practices used with an A1 refrigerant (R-410A) to those needed with an A2L (R-32 or R-454B).

Figure 1
There are many tool manufacturers ready to supply dependable A2L products today. While I am not recommending any particular brand, it is worth it to purchase high quality equipment thus ensuring reliable performance over the long run.
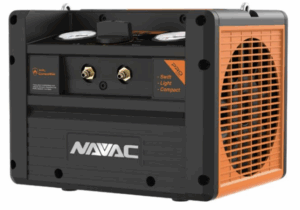
Figure 2: This NAVAC recovery machine is A2L compliant. (Photo credit: NAVAC)
A NAVAC recovery machine, for example (Figure 2), is A2L compliant by virtue of its inherent protection features: sparkless design; DC brushless motor; soft contact power switches; covered connections for all electrical terminations; and internal fan included.
The Yellow Jacket A2L complaint vacuum pump (Figure 3) also has important features allowing for the unit to operate in close proximity to the A2L installation.

Figure 3: This Yellow Jacket vacuum heat pump meets A2L compliance. (Photo credit: Yellow Jacket)
These features include high torque, brushless DC motor; lighter than AC motor pumps; non sparking switch; oil reservoir port doubles as a pump exhaust – threaded to attach garden hose exhausting to a remote location; locking power cord connection to prevent arcing due to accidental disconnection.
While it is not required to use an A2L compliant pump if the unshielded switch and vent are away from the work area (10 feet is suggested), a compliant pump allows the use of a short vacuum hose that should help to uncomplicate the dehydration and evacuation procedure. Leak detectors must also be A2L compliant, many updated units are already on the market.
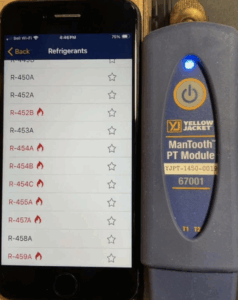
Figure 4: Updated app for the author’s 10-year-old gauge includes data for a variety of A2L refrigerants.
Electronic gauge manifolds available from a variety of manufacturers may or may not be upgradable to deal with A2L refrigerant data. Be sure to check with your manufacturer for A2L updates.
I checked my Mantooth gauge purchased 10 years ago and discovered the supporting app has been updated with data for a variety of A2L refrigerants. (Figure 4).
The Techniques
While not essentially new, as industry professionals have been working with sealed systems all along, A2L practices will require a heighted attention to detail. Technicians will be faced with servicing equipment containing R-22 with mineral oil to R-410A and A2L systems containing POE oil.
While traditional gauge sets will still be useful at initial system commissioning and after a system repair, with today’s technological alternatives, a bulky gauge set may not always be the best choice for accurate charging results.
Many experts are advising against connecting a gauge set every time a low system refrigerant charge is suspected.
Gary McCreadie, owner of the HVAC Know It All website, posted a podcast interview with engineer Jim Bergmann about how to verify system charge without using the traditional invasive method of first “slapping on the gauges.”
When parameters such as superheat/subcool and discharge line temperature ring true, then the technician may decide to avoid invasive testing thus avoiding some loss of charge and potential system contamination from the residue of “stuff” leftover in hoses.
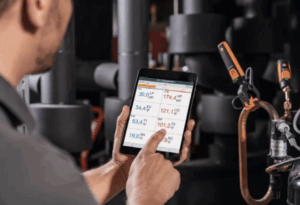
Figure 5: Wireless probes in action. (Photo credit: Testo)
Should an evaluation of the system charge be necessary, consider using low loss wireless probes now widely available (Figure 5).
Yes, I know, working with an app can be problematic, especially outdoors in the bright sunshine. Some systems, equipped with pressure transducers, allow technicians to read system pressures using a DC voltmeter directly from a control board. Other units might include a communicating display within the unit or permit remote reporting that send data directly to the servicer.
Using digital data collection means the refrigeration system will remain unaffected unless absolutely necessary.
What Else Is Different?
As always, due diligence according to manufacturer’s installation instructions and industry standards are paramount to achieving successful A2L equipment installations and efficient servicing.
While I am all in for safety, that includes protection of the public and HVAC/R personnel, I should note that many residential applications have an extremely flammable A3 quasi refrigerant (namely natural gas/methane [R-50] or propane [R-290]) already flowing to appliances for decades using a simple chemical odorant as a mitigation strategy. Nevertheless, companies will be required to ensure the conditioned space is large enough and contains enough air to maintain the indoor atmosphere below the lower flammability limit (LFL) should the entire system charge leak into the conditioned space.
Thus, exhibiting an abundance of caution, manufacturer’s instructions will identify the maximum allowable charge for every AHRI matched system installation. These charge values are not universal and will vary by application. One HVAC industry standard, the updated version of UL60335-2-40, provides the safety requirements for household and similar A2L charged appliances, including air conditioners, heat pumps, and dehumidifiers.
This standard specifies the necessary ventilation measures to ensure safety in the event of a refrigerant leak. The standard places charge limitations on indoor spaces and manufacturers will have distilled the standards into appropriate charts in their literature.
Charge Limits:
- For unventilated spaces (m1 charge) is the amount of refrigerant that can be used without additional ventilation measures.
- For ventilated spaces (m2 charge for residential applications) requires systems to include ventilation measures to ensure any leaked refrigerant is dispersed and diluted. Manufacturers will supply an evaporator coil leak sensor and control board. Should the sensor detect a significant leak and report it to the control board (diffusion control), gas/electric heating will stop, and the furnace fan will operate at an appropriate diffusion speed.
- For larger applications (m3 charges) such systems will require more extensive ventilation and other mitigation measures including additional sensors, alarms and control systems to manage refrigerant leaks.
Accessories such as electronic air purifiers may require an airflow sensing kit; HRV/ERV equipment should be checked ensure the unit will not recirculate air meant for proper diffusion.
Auxiliary devices must not be a potential ignition source.
I read one manufacturer’s chart in which an AHRI matched 3-ton split system had the A2L charge limit related to space size and necessary mitigation airflow: 3-ton A2L heat pump unit; max. total system charge—205.70 ounces (5.83 kg); min. conditioned space size—185.87 sq. ft. (17.27 sq. m.); min. mitigation airflow: 335.40 cfm.
Since a 3-ton unit is likely to be installed in a space much larger than 185 sq. ft., I believe most regular AC or heat pump installations with simple line sets will be within range of m2 requirements.
Servicing Guidelines
Ensure all refrigerant has been removed from the system or isolated by shut off valves before opening for repair or replacement of parts. Manufacturer requirements are universal in this regard:
- Recommended to have a 10-foot work perimeter with no ignition sources (e.g., gas water heater in service), no other flammable vapours, and where an exit point cannot be readily utilized. Wear proper PPE.
- Be sure the area is adequately ventilated prior to opening the system.
- Have a CO2 or dry powder fire extinguisher nearby.
- Recover the charge down to atmosphere (0 psig) and weigh the A2L refrigerant into an appropriately marked recovery cylinder.
- Keep the CCH on, run the air handler fan, use a heating banket to be sure liquid A2L trapped in the system is vaporized and removed.
- A dry nitrogen purge is required, see manufacturer chart for purge times.
- Brazing-in new components (flow nitrogen at 3 – 5 CuFt/hr) is typically required, check with manufacturer for approval to use press fit connections.
- Pressure/leak testing followed by deep evacuation to less than 500 microns is required. The deep vacuum decay test should indicate no vacuum to creep above manufacturer’s minimum standard within mandated time limit.
It must be stressed that long-standing HVAC/R practices and procedures still predominate. Improve your knowledge and sharpen your skills by taking advantage of all available A2L training. HRAI is offering on-line training programs.
An ancient idiom sums up A2Ls nicely: “Things are the same, only different.” All you need to do is to learn the different parts. <>
Ian McTeer is an HVAC consultant with over 35 years of experience in the industry. He was a field rep for Trane Canada. McTeer is a refrigeration mechanic and Class 1 Gas technician. He can be reached at imcteer@outlook.com.